Top 10 Best Conveyor Systems:
In today’s fast-paced manufacturing and logistics industries, conveyor systems play a crucial role in the efficient movement of goods and materials. Best conveyor systems are used to transport a wide range of products, from raw materials to finished goods, and are commonly used in various industries such as food processing, automotive, pharmaceuticals, and more. This article will explore the different types of best conveyor systems, their features, advantages, disadvantages, and frequently asked questions.
Which conveyor is most efficient?
The efficiency of a conveyor depends on the specific application and requirements. However, some commonly recognized efficient best conveyor systems include belt conveyors, roller conveyors, and overhead conveyors. These systems are widely used in various industries and offer high efficiency for different types of material handling tasks.
How do I choose a conveyor system?
Choosing the right conveyor system involves considering various factors specific to your application. Here are some key steps to guide you in the selection process:
Identify your specific material handling requirements, such as load type, size, weight, and throughput needs.
Determine the layout and space constraints of your facility.
Consider the type of material to be transported (e.g., bulk materials, packages, delicate items) and their handling characteristics.
Assess any environmental factors that may affect the conveyor system, such as temperature, humidity, or cleanliness requirements.
Evaluate the cost-effectiveness and return on investment (ROI) of different conveyor options.
Research and consult with reputable conveyor manufacturers or system integrators to get expert advice tailored to your needs.
Belt Conveyor Systems:
Belt Conveyors: Belt conveyors are the most common type of conveyor system and use a belt to transport products or materials along a straight or curved path. They are versatile and can be used in a variety of industries.
Roller Conveyors: Roller conveyors use a series of rollers to move products or materials along a straight path. They are ideal for handling heavier items and are often used in warehouses and distribution centers.
Chain Conveyors: Chain conveyors use chains to move products or materials along a straight or curved path. They are commonly used in the automotive industry to move car parts through the manufacturing process.
Screw Conveyors: Screw conveyors use a rotating screw to move products or materials along a straight or inclined path. They are commonly used in the food processing industry to move bulk materials such as grains and flour.
Pneumatic Conveyors: Pneumatic conveyors use air pressure to move products or materials through a pipe or tube. They are commonly used in the chemical industry to transport powders and other dry materials.
Overhead Conveyors: Overhead conveyors use a track system to move products or materials along a path that is above the ground. They are often used in the automotive industry to move car parts through the manufacturing process.
Vibrating Conveyors: Vibrating conveyors use vibrations to move products or materials along a path. They are commonly used in the food processing industry to transport sticky or delicate materials.
Bucket Conveyors: Bucket conveyors use buckets to transport products or materials along a path. They are commonly used in the mining industry to transport materials such as coal and gravel.
Magnetic Conveyors: Magnetic conveyors use magnets to transport products or materials along a path. They are commonly used in the metalworking industry to move metal parts through the manufacturing process.
Spiral Conveyors: Spiral conveyors use a spiral path to transport products or materials along a path. They are commonly used in the food processing industry to move products through different levels of a facility.
Belt Conveyors
Belt conveyors are one of the most widely used types of conveying equipment in the world. They are used to move materials from one point to another in a continuous and efficient manner. Belt conveyors are used in a variety of industries, including mining, agriculture, food processing, pharmaceuticals, and many others.
Features of Belt Conveyors:
- Belt conveyors are versatile and can be used to transport a wide range of materials.
- They can be designed to operate in a horizontal, inclined, or declined position.
- Belt conveyors can be designed to handle heavy-duty loads.
- They are energy-efficient and require minimal maintenance.
- Belt conveyors can be used for both short and long distances.
- They are easy to install and can be configured to meet specific needs.
- Belt conveyors are cost-effective and provide a high return on investment.
- They can be used to transport materials at high speeds.
- Belt conveyors can be used to transport materials at low speeds.
- They can be equipped with a variety of accessories, including transfer chutes, hoppers, and loading devices.
- Belt conveyors can be designed to handle hazardous materials.
- They can be designed to handle materials at high temperatures.
- Belt conveyors can be designed to handle materials at low temperatures.
- They can be designed to handle wet or dry materials.
- Belt conveyors can be designed to handle abrasive materials.
- They can be designed to handle sticky materials.
- Belt conveyors can be designed to handle materials of different sizes and shapes.
- They can be designed to operate in a variety of environments, including indoor and outdoor environments.
- Belt conveyors can be designed to operate in cleanroom environments.
- They can be designed to operate in explosive environments.
- Belt conveyors can be designed to operate in corrosive environments.
- They can be designed to operate in high-pressure environments.
- Belt conveyors can be designed to operate in low-pressure environments.
- They can be designed to operate in high-humidity environments.
- Belt conveyors can be designed to operate in low-humidity environments.
Advantages of Belt Conveyors:
- Belt conveyors are efficient and can move materials quickly and easily.
- They are cost-effective and provide a high return on investment.
- Belt conveyors are versatile and can be used to transport a wide range of materials.
- They are easy to install and can be configured to meet specific needs.
- Belt conveyors are energy-efficient and require minimal maintenance.
- They can be used to transport materials at high speeds.
- Belt conveyors can be used to transport materials at low speeds.
- They are safe and can be designed to meet specific safety requirements.
- Belt conveyors are reliable and can be designed to operate continuously.
- They can be used to transport materials over long distances.
- Belt conveyors can be designed to handle materials of different sizes and shapes.
- They can be designed to operate in a variety of environments.
- Belt conveyors can be designed to handle hazardous materials.
- They can be designed to handle materials at high temperatures.
- Belt conveyors can be designed to handle materials at low temperatures.
Disadvantages of Belt Conveyors:
- Belt conveyors can be expensive to install.
- They can be difficult to maintain, especially if they are used to transport abrasive or sticky materials.
- Belt conveyors can be noisy and can cause vibration.
- They may not be suitable for transporting materials that …are too fragile or delicate.
- Belt conveyors may not be suitable for applications that require precise positioning of materials.
FAQs about Belt Conveyors:
What is a belt conveyor?
A belt conveyor is a machine used to move materials from one point to another on a continuous belt.
What are the components of a belt conveyor?
A belt conveyor typically consists of a belt, pulleys, idlers, and a motor.
What are the different types of belt conveyors?
The different types of belt conveyors include flat belt conveyors, troughed belt conveyors, and sidewall belt conveyors.
What materials can be transported using a belt conveyor?
Belt conveyors can be used to transport a wide range of materials, including food products, agricultural products, minerals, chemicals, and more.
What are the advantages of using a belt conveyor?
The advantages of using a belt conveyor include their versatility, energy efficiency, low maintenance requirements, and ability to handle a wide range of materials.
What are the disadvantages of using a belt conveyor?
The disadvantages of using a belt conveyor include their cost, maintenance requirements, noise and vibration, and limitations in transporting delicate materials.
What safety features should be included in a belt conveyor?
Safety features that should be included in a belt conveyor include emergency stop buttons, guarding around moving parts, and warning signs and labels.
What maintenance is required for a belt conveyor?
Maintenance requirements for a belt conveyor include regular cleaning, lubrication of moving parts, and inspection for wear and damage.
What factors should be considered when designing a belt conveyor?
Factors that should be considered when designing a belt conveyor include the type and size of materials being transported, the distance to be covered, and the environmental conditions in which the conveyor will operate.
What is the maximum distance that a belt conveyor can transport materials?
The maximum distance that a belt conveyor can transport materials depends on a variety of factors, including the type and size of materials being transported, the speed of the conveyor, and the power of the motor driving the conveyor.
Can a belt conveyor be used to transport materials up an incline?
Yes, a belt conveyor can be designed to transport materials up an incline, although the design of the conveyor will need to be adjusted to account for the change in elevation.
Can a belt conveyor be used to transport materials down an incline?
Yes, a belt conveyor can be designed to transport materials down an incline, although special precautions will need to be taken to prevent the materials from sliding down the incline too quickly.
What is the maximum speed that a belt conveyor can travel?
The maximum speed that a belt conveyor can travel depends on a variety of factors, including the size and type of belt, the weight and size of the materials being transported, and the power of the motor driving the conveyor.
How are belt conveyors powered?
Belt conveyors are typically powered by electric motors, which drive the pulleys that move the belt.
Can belt conveyors be used in food processing applications?
Yes, belt conveyors can be designed to meet the specific requirements of food processing applications, including the use of food-grade materials and compliance with food safety regulations.
Can belt conveyors be used in cleanroom environments?
Yes, belt conveyors can be designed to meet the specific requirements of cleanroom environments, including using materials that are easy to clean and maintain.
Can belt conveyors be used in explosive environments?
Yes, belt conveyors can be designed to meet the specific requirements of explosive environments, including using explosion-proof motors and components.
Can belt conveyors be used to transport hazardous materials?
Yes, belt conveyors can be designed to meet the specific requirements of transporting hazardous materials, including the use of specialized belts and components.
What is the cost of a belt conveyor?
The cost of a belt conveyor can vary widely depending on the size, type, and complexity of the conveyor, as well as the materials and components used.
Can belt conveyors be customized to meet specific requirements?
Yes, belt conveyors can be customized to meet specific requirements, including the size and shape of the conveyor, the type and size of materials being transported, and the environmental conditions in which the conveyor will operate.
What are some common applications of belt conveyors?
Common applications of belt conveyors include manufacturing, food processing, agriculture, mining, and transportation.
How do belt conveyors compare to other types of conveyors?
Belt conveyors are generally more versatile and energy-efficient than other types of conveyors, although they may not be suitable for all applications.
Can belt conveyors be used to sort materials?
Yes, belt conveyors can be designed to sort materials using a variety of mechanisms, including diverters and sorting belts.
How do belt conveyors handle curves and corners?
Belt conveyors can be designed to handle curves and corners using specialized belts and components, such as curved belts and corner rollers.
What are the environmental benefits of using belt conveyors?
The environmental benefits of using belt conveyors include their energy efficiency, which can reduce greenhouse gas emissions, as well as their ability to transport materials in a controlled and efficient manner, which can reduce waste and pollution.
Conclusion:
Belt conveyors are versatile and efficient tools for moving materials in a variety of industries. With their ability to handle a wide range of materials, distances, and environmental conditions, they are a popular choice for manufacturing, food processing, mining, and transportation applications. While they do have some disadvantages, such as high maintenance requirements and limitations in transporting delicate materials, these can often be addressed through proper design and maintenance. Overall, belt conveyors offer many advantages over other types of conveyors, including their energy efficiency, low maintenance requirements, and ability to handle a wide range of materials.
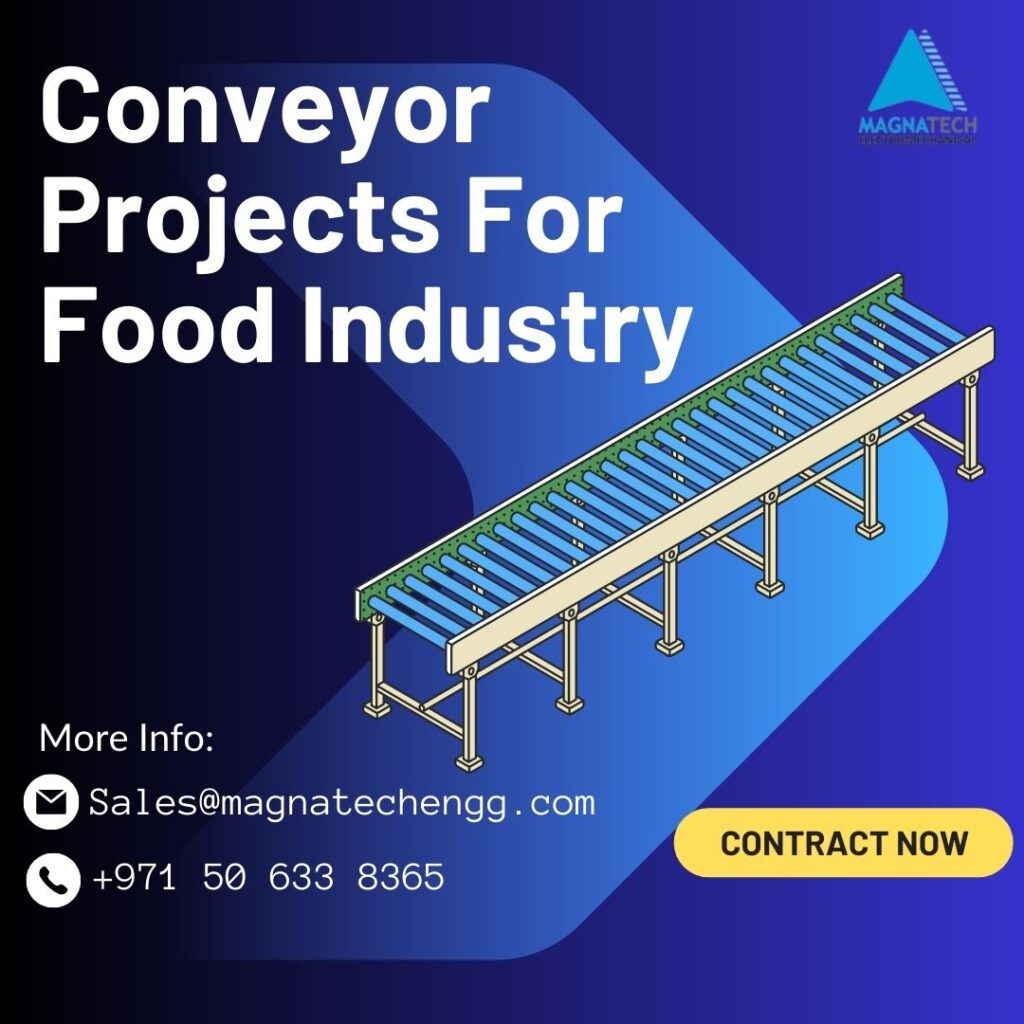
Roller conveyor chain
Roller conveyors are an essential piece of equipment in the manufacturing and distribution industry. They are used to move materials from one point to another, and their design allows for the easy loading and unloading of goods. Roller conveyors are widely used in industries such as automotive, food and beverage, packaging, and logistics. The primary function of a roller conveyor is to transport goods quickly and efficiently, thus saving time and increasing productivity.
Features:
- Roller conveyors consist of a series of rollers that are mounted on a frame and powered by a motor.
- They are available in different widths and lengths, making them adaptable to various applications.
- Roller conveyors can be customized to suit the specific needs of a business, allowing for optimal efficiency.
- They are designed to transport goods of different shapes and sizes, making them suitable for a wide range of industries.
- Roller conveyors can be used in both straight and curved configurations, making them versatile.
- They can be used to transport goods both horizontally and vertically, making them flexible.
- Roller conveyors are durable and require minimal maintenance, making them cost-effective in the long run.
- They can be designed with different materials such as steel, plastic, or aluminum, allowing for a range of load capacities.
- Roller conveyors can be fitted with safety features such as emergency stop buttons, sensors, and safety guards.
- They are easy to install and can be integrated with other equipment in a production line.
- Roller conveyors are energy-efficient, as they use less power than other best conveyor systems.
- They can be operated manually or automated, depending on the needs of the business.
- Roller conveyors are designed to withstand harsh environments, such as extreme temperatures or wet conditions.
- They can be used to transport goods both indoors and outdoors, making them versatile.
- Roller conveyors can be used to transport fragile items, as they provide a smooth and stable surface.
- They can be used to transport heavy loads, as they are designed to withstand high-weight capacities.
- Roller conveyors can be used to transport goods over long distances, reducing the need for manual labor.
- They can be used to transport goods at a high speed, increasing productivity and efficiency.
- Roller conveyors can be used to transport goods at a low speed, allowing for easy loading and unloading.
- They can be used to accumulate goods, allowing for better control of the production line.
- Roller conveyors can be used to sort goods, reducing the need for manual labor.
- They can be used to merge or divert goods, allowing for a smoother flow of goods in a production line.
- Roller conveyors can be used to stack goods, reducing the need for manual labor.
- They can be used to buffer goods, allowing for better control of the production line.
- Roller conveyors can be used to transport goods in a straight line or in a curved path, allowing for a range of production line configurations.
Advantages:
- Roller conveyors are cost-effective in the long run, as they require minimal maintenance and can be customized to suit the specific needs of a business.
- They increase productivity and efficiency, as they transport goods quickly and smoothly.
- Roller conveyors are easy to install and can be integrated with other equipment in a production line, reducing downtime.
- They are energy-efficient, as they use less power than other best conveyor systems, reducing energy costs.
- Roller conveyors are versatile, as they can be used to transport goods of different shapes and sizes, both horizontally and vertically
- Roller conveyors are reliable, as they are designed to withstand harsh environments and can transport goods over long distances.
- They provide a smooth and stable surface, making them suitable for transporting fragile items.
- Roller conveyors reduce the need for manual labor, as they can transport goods at high speeds and accumulate goods.
- They can be used to sort, merge, divert, stack, and buffer goods, allowing for a smoother flow of goods in a production line.
- Roller conveyors can be operated manually or automated, depending on the needs of the business, providing flexibility.
- They can be designed with different materials, allowing for a range of load capacities and customization options.
- Roller conveyors can be fitted with safety features, reducing the risk of accidents and increasing workplace safety.
- They can be used to transport goods both indoors and outdoors, making them suitable for a wide range of industries.
- Roller conveyors can be used to transport heavy loads, reducing the need for manual labor and increasing productivity.
- They can be used to transport goods at a low speed, allowing for easy loading and unloading, and reducing the risk of damage to goods.
Disadvantages:
- Roller conveyors can be noisy, which may be a concern in certain environments.
- They may require regular cleaning to prevent the buildup of debris or dust, which can affect the smooth operation of the rollers.
- Roller conveyors may not be suitable for transporting goods that require a flat surface.
- They may require a larger amount of space compared to other best conveyor systems, which may be a limitation in certain facilities.
- Roller conveyors may require a higher initial investment compared to other best conveyor systems, which may be a concern for small businesses.
FAQs & Answers:
What are roller conveyors used for?
Roller conveyors are used to transport goods from one point to another in a production line or warehouse.
What types of roller conveyors are available?
There are various types of roller conveyors available, including gravity roller conveyors, powered roller conveyors, and accumulation roller conveyors.
What materials are roller conveyors made of?
Roller conveyors can be made of various materials, including steel, plastic, or aluminum.
How do roller conveyors work?
Roller conveyors consist of a series of rollers that rotate on a frame and transport goods along the conveyor.
What are the benefits of roller conveyors?
Roller conveyors increase productivity, reduce manual labor, are cost-effective in the long run, and can transport goods of different shapes and sizes.
How do you maintain roller conveyors?
Roller conveyors require minimal maintenance, but regular cleaning and inspection are recommended to ensure smooth operation.
What is the weight capacity of roller conveyors?
The weight capacity of roller conveyors depends on the design and materials used, but they can transport heavy loads.
What industries use roller conveyors?
Roller conveyors are used in a wide range of industries, including automotive, food and beverage, packaging, and logistics.
How do you choose the right roller conveyor for your business?
The right roller conveyor for your business will depend on your specific needs and the type of goods you need to transport.
Can roller conveyors be customized?
Yes, roller conveyors can be customized to suit the specific needs of your business.
How do you install roller conveyors?
Roller conveyors are easy to install and can be integrated with other equipment in a production line.
How do roller conveyors save time?
Roller conveyors transport goods quickly and smoothly, reducing the need for manual labor and increasing productivity.
Chain Conveyors
Chain conveyors are a popular type of mechanical conveyor system used in various industrial applications. They are designed to transport heavy materials or products across long distances. Chain conveyors use a continuous chain loop that moves on a set of sprockets to move materials from one place to another. These conveyors are suitable for various industries such as automotive, agriculture, food and beverage, construction, and many more.
Features of Chain Conveyors:
- Chain conveyors use a continuous chain loop to transport materials or products.
- They are suitable for heavy-duty applications and can handle high loads.
- Chain conveyors can be designed for various inclines, declines, or horizontal applications.
- They can be used for various shapes and sizes of materials, including irregular shapes and bulky products.
- Chain conveyors are ideal for transporting materials across long distances.
- They can be designed to operate in harsh environments, including high temperatures, humid, and dusty environments.
- Chain conveyors can be customized to suit specific applications and industry requirements.
- They are available in various chain types, including roller chains, engineering plastic chains, and stainless steel chains.
- Chain conveyors can be designed to operate at various speeds to suit specific applications.
- They can be fitted with various attachments, including cleats, side guards, and product stops.
- Chain conveyors require minimal maintenance and have low operating costs.
- They are easy to install and require minimal space.
- Chain conveyors can be designed to be reversible for the bi-directional transport of materials.
- They can be designed to operate at various temperatures, including freezing and high-temperature applications.
- Chain conveyors can be designed for various load capacities, including light-duty, medium-duty, and heavy-duty applications.
- They are ideal for handling delicate products without damage.
- Chain conveyors can be designed for various angles, including vertical and horizontal transport.
- They can be designed to transport products with different heights, widths, and weights.
- Chain conveyors can be fitted with sensors to control the flow of materials.
- They can be designed to be noiseless during operation.
- Chain conveyors are energy-efficient and cost-effective.
- They are easy to clean and maintain.
- Chain conveyors can be designed to comply with various safety regulations.
- They can be designed to be automated for efficient and high-volume material handling.
- Chain conveyors have a long service life and are durable.
Advantages of Chain Conveyors:
- Chain conveyors are suitable for heavy-duty applications and can handle high loads.
- They are ideal for transporting materials across long distances.
- Chain conveyors can be designed to operate in harsh environments.
- They require minimal maintenance and have low operating costs.
- They are easy to install and require minimal space.
- Chain conveyors can be designed to be reversible for the bi-directional transport of materials.
- They are ideal for handling delicate products without damage.
- Chain conveyors can be designed for various angles, including vertical and horizontal transport.
- They are energy-efficient and cost-effective.
- They are easy to clean and maintain.
- Chain conveyors can be designed to comply with various safety regulations.
- They can be designed to be automated for efficient and high-volume material handling.
- Chain conveyors have a long service life and are durable.
- They can be customized to suit specific applications and industry requirements.
- Chain conveyors can improve efficiency and productivity in manufacturing and material handling operations.
Disadvantages of Chain Conveyors:
- Chain conveyors can be noisy during operation, which can be a nuisance for workers.
- They can be challenging to clean when transporting dusty or dirty materials.
- Chain conveyors require regular lubrication to ensure smooth operation and prevent wear and tear.
- They may not be suitable for transporting fragile or lightweight materials that may get caught in the chain.
- Chain conveyors may require frequent inspections to ensure that the chain and sprockets are in good condition.
FAQs & Ans:
- Which conveyor is most efficient?
- The efficiency of a conveyor depends on various factors such as the specific application, load characteristics, and operating conditions. However, some commonly recognized efficient best conveyor systems include belt conveyors, roller conveyors, and overhead conveyors.
- What are the best conveyor belt companies?
- There are several well-regarded conveyor belt companies that offer high-quality products and solutions. Some of the notable ones include Habasit AG, Intralox LLC, Forbo Movement Systems, Ammeraal Beltech, and Fenner Dunlop Conveyor Belting. These companies provide a wide range of conveyor belt options suitable for different industries.
- How do I choose a conveyor system?
- When choosing a conveyor system, consider factors such as your specific material handling requirements, facility layout and space constraints, the type of material to be transported, environmental factors, and cost-effectiveness. It is advisable to research and consult with reputable conveyor manufacturers or system integrators to get expert advice tailored to your needs.
- What is the most used conveyor?
- Belt conveyors are one of the most commonly used conveyors across various industries. They offer versatility, high load-carrying capacity, and are suitable for horizontal or inclined transportation over long distances. Belt conveyors are widely used in industries such as mining, manufacturing, logistics, and food processing.
What is a chain conveyor?
A chain conveyor is a mechanical conveyor system that uses a continuous chain loop to transport materials or products from one place to another.
What are chain conveyors used for?
Chain conveyors are used in various industrial applications, including manufacturing, mining, agriculture, construction, and many more. They are suitable for transporting heavy and bulky materials across long distances.
How does a chain conveyor work?
A chain conveyor uses a continuous chain loop that moves on a set of sprockets. The chain loop is fitted with attachments such as cleats, side guards, or product stops that grip and transport materials or products along the conveyor.
What are the types of chain conveyors?
The types of chain conveyors include roller chain conveyors, engineering plastic chain conveyors, and stainless steel chain conveyors.
What are the benefits of using chain conveyors?
Chain conveyors are suitable for heavy-duty applications, can handle high loads, and can be customized to suit specific applications and industry requirements. They are also energy-efficient, cost-effective, and have a long service life.
What materials can be transported using a chain conveyor?
Chain conveyors can transport a wide range of materials, including bulk materials, pallets, crates, boxes, and bags.
What industries use chain conveyors?
Various industries use chain conveyors, including automotive, food and beverage, mining, construction, and many more.
Can chain conveyors operate in harsh environments?
Yes, chain conveyors can be designed to operate in harsh environments, including high temperatures, humid, and dusty environments.
How much maintenance do chain conveyors require?
Chain conveyors require minimal maintenance and have low operating costs. However, they require regular lubrication to ensure smooth operation and prevent wear and tear.
How do you install a chain conveyor?
Installing a chain conveyor requires mounting the conveyor frame, aligning the sprockets, fitting the chain onto the sprockets, and adjusting the tension of the chain.
Can chain conveyors transport delicate products?
Yes, chain conveyors can be designed to transport delicate products without damage.
How fast can chain conveyors operate?
Chain conveyors can be designed to operate at various speeds to suit specific applications.
Can chain conveyors transport materials at an incline or decline?
Yes, chain conveyors can be designed for various inclines, declines, or horizontal applications.
Can chain conveyors be designed to transport products of different heights and widths?
Yes, chain conveyors can be designed to transport products with different heights, widths, and weights.
How do you clean a chain conveyor?
Cleaning a chain conveyor involves removing any debris, dirt, or dust from the conveyor and lubricating the chain and sprockets.
What safety precautions should you take when operating a chain conveyor?
Operators should follow safety procedures, such as wearing protective gear and avoiding loose clothing. Additionally, chain conveyors should comply with various safety regulations.
How do you troubleshoot a chain conveyor?
Common issues with chain conveyors include chain breakage, excessive chain wear or stretching, sprocket wear, and misalignment. To troubleshoot a chain conveyor, operators should inspect the chain, sprockets, and other components for damage or wear and make necessary adjustments or replacements.
Can chain conveyors be automated?
Yes, chain conveyors can be automated using sensors, control systems, and other technology to improve efficiency and productivity.
What is the difference between a chain conveyor and a belt conveyor?
A chain conveyor uses a continuous chain loop to transport materials, while a belt conveyor uses a continuous belt. Chain conveyors are typically used for heavy-duty applications and can handle high loads, while belt conveyors are suitable for lighter loads.
What is the difference between a chain conveyor and a screw conveyor?
A chain conveyor uses a continuous chain loop to transport materials, while a screw conveyor uses a rotating helical screw to move materials. Chain conveyors are typically used for horizontal or inclined transportation, while screw conveyors are suitable for vertical transportation.
What is the difference between a chain conveyor and a slat conveyor?
A chain conveyor uses a continuous chain loop to transport materials, while a slat conveyor uses a series of interlocking slats. Chain conveyors are typically used for heavy-duty applications and can handle high loads, while slat conveyors are suitable for lighter loads.
How do you choose the right chain conveyor for your application?
Choosing the right chain conveyor for your application involves considering factors such as the type and size of materials being transported, the distance and speed of transport, and any special requirements or industry regulations.
Can chain conveyors be customized?
Yes, chain conveyors can be customized to suit specific applications and industry requirements, such as adding cleats, side guards, or product stops.
What is the maximum load capacity of a chain conveyor?
The maximum load capacity of a chain conveyor depends on factors such as the size of the conveyor, the type and weight of the materials being transported, and the speed of transport.
How do you maintain a chain conveyor?
Maintaining a chain conveyor involves regular lubrication, inspecting and replacing worn or damaged components, and cleaning the conveyor.
Conclusion:
Chain conveyors are versatile, cost-effective, and efficient mechanical systems used in various industries for material handling and transportation. With the ability to handle heavy loads and customizable design options, chain conveyors can increase productivity and improve efficiency in manufacturing and industrial operations. While there are some disadvantages and maintenance requirements, the advantages of using chain conveyors outweigh the potential drawbacks. With proper care and maintenance, chain conveyors can provide a long-lasting and reliable solution for transporting materials and products.
Best conveyor systems
Screw conveyors are an essential tool in the manufacturing, processing, and packaging industries. They are used for moving granular, powder, and liquid materials from one place to another in a controlled manner. Screw conveyors are designed to handle a wide range of materials and can be used for horizontal, inclined, and vertical conveying.
Features of Screw Conveyors:
- Screw conveyors are versatile and can be used for horizontal, inclined, and vertical conveying.
- They can be customized to fit the specific needs of a project.
- Screw conveyors are efficient and can move materials quickly.
- They are easy to maintain and require minimal downtime for repairs.
- Screw conveyors can handle a wide range of materials, including powders, granules, and liquids.
- They can be used in various industries, including food, chemical, and pharmaceuticals.
- Screw conveyors are available in various sizes and capacities to suit different needs.
- They are constructed from durable materials, such as stainless steel or carbon steel.
- Screw conveyors can be designed for continuous or intermittent operation.
- They can be designed to handle abrasive or corrosive materials.
- Screw conveyors can be designed to be self-cleaning, reducing maintenance costs.
- They can be designed to be explosion-proof for use in hazardous environments.
- Screw conveyors are easy to install and require minimal setup time.
- They can be designed to handle high-temperature materials.
- Screw conveyors can be designed to handle materials with high moisture content.
- They can be designed with various discharge options, including rotary valves, slide gates, and screw feeders.
- Screw conveyors can be designed to convey materials over long distances.
- They can be designed to be reversible, allowing materials to be conveyed in either direction.
- Screw conveyors can be designed to handle materials with a wide range of densities.
- They can be designed to handle materials with a wide range of particle sizes.
- Screw conveyors can be designed to handle materials with a wide range of viscosities.
- They can be designed with multiple inlets and outlets for feeding and discharging materials.
- Screw conveyors can be designed to operate at high speeds.
- They can be designed to operate at low noise levels.
- Screw conveyors can be designed to meet food-grade standards.
Advantages of Screw Conveyors:
- Screw conveyors are cost-effective and can save money on labor costs.
- They can be used to automate material handling processes, increasing efficiency.
- Screw conveyors can reduce material waste and improve product quality.
- They can be used to create a more hygienic working environment.
- Screw conveyors can reduce the risk of material contamination.
- They can be used to increase production rates.
- Screw conveyors can be used to transport materials to hard-to-reach areas.
- They can be used to convey materials at high temperatures without causing damage.
- Screw conveyors can be designed to reduce the risk of material segregation.
- They can be designed to handle materials with minimal product degradation.
- Screw conveyors can be used to move materials vertically, reducing the need for additional equipment.
- They can be designed to reduce energy consumption.
- Screw conveyors can be used to move materials gently, reducing the risk of damage.
- They can be used to control the flow rate of materials.
- Screw conveyors can be designed to meet various safety standards.
Disadvantages of Screw Conveyors:
- Screw conveyors can be difficult to clean and maintain if they are not designed properly.
- They can generate dust or fumes during operation, which can be hazardous to workers’ health.
- Screw conveyors may not be suitable for conveying materials that are extremely fragile or prone to breaking apart.
- They can be noisy during operation, which can be disruptive to workers or nearby residents.
- Screw conveyors can be expensive to install if they require significant customization or modifications.
FAQs & Answers about Screw Conveyors:
What is a screw conveyor?
A screw conveyor is a machine used to move materials from one place to another in a controlled manner. It consists of a rotating screw inside a tube or trough.
What materials can be conveyed with a screw conveyor?
Screw conveyors can handle a wide range of materials, including powders, granules, and liquids. Some common materials include cement, grains, sugar, and chemicals.
What are the different types of screw conveyors?
The different types of screw conveyors include horizontal, inclined, and vertical conveyors. They can also be designed to be flexible, shaftless, or auger conveyors.
What factors should be considered when selecting a screw conveyor?
Factors to consider when selecting a screw conveyor include the material being conveyed, the capacity required, the operating environment, and the required speed and torque.
How are screw conveyors designed?
Screw conveyors are designed based on the specific needs of a project, taking into account factors such as material type, conveyor capacity, and the operating environment. The design process typically involves engineering calculations and simulations.
What are the main components of a screw conveyor?
The main components of a screw conveyor include the screw, the trough or tube, the motor and gearbox, and the discharge mechanism.
What is the function of the screw in a screw conveyor?
The screw is the primary component of a screw conveyor, and its function is to move materials from one end of the conveyor to the other.
How are screw conveyors powered?
Screw conveyors are typically powered by electric motors, which are connected to the screw via a gearbox or direct drive system.
Can screw conveyors be used for both horizontal and vertical conveying?
Yes, screw conveyors can be designed for both horizontal and vertical conveying, as well as inclined to convey.
What is the capacity range of screw conveyors?
Screw conveyors can be designed to handle a wide range of capacities, from a few pounds per hour to several hundred tons per hour.
What is the maximum distance that a screw conveyor can convey materials?
The maximum distance that a screw conveyor can convey materials depends on various factors, including the material being conveyed, the conveyor capacity, and the operating environment. In general, screw conveyors can be designed to convey materials over long distances.
Can screw conveyors be used to convey abrasive materials?
Yes, screw conveyors can be designed to handle abrasive materials, such as sand or gravel.
How are screw conveyors cleaned and maintained?
Screw conveyors can be cleaned and maintained by flushing the system with water or air and inspecting the components for wear or damage. Regular maintenance and cleaning can help prevent issues and prolong the life of the conveyor.
Can screw conveyors be used in hazardous environments?
Yes, screw conveyors can be designed to be explosion-proof and used in hazardous environments, such as those with flammable or explosive materials.
What safety measures should be taken when using a screw conveyor?
Safety measures when using a screw conveyor include ensuring that workers are trained in its safe operation, providing proper guarding, and following all safety guidelines and regulations.
Can screw conveyors be used in the food industry?
Yes, screw conveyors can be designed to meet food industry standards, with features such as sanitary construction and easy-to-clean components.
What are some common applications for screw conveyors?
Common applications for screw conveyors include transporting materials in bulk, feeding and metering materials into processing equipment, and moving materials between different processing stages.
What industries use screw conveyors?
Screw conveyors are used in a wide range of industries, including agriculture, mining, chemical processing, food and beverage, and wastewater treatment.
What are some common design options for screw conveyors?
Design options for screw conveyors include different screw designs, such as helicoid and sectional flights, as well as different discharge options, such as slide gates and valves.
Can screw conveyors be customized for specific applications?
Yes, screw conveyors can be customized to meet the specific needs of a project, with options for materials of construction, capacity, and other features.
What are some advantages of using screw conveyors over other conveying methods?
Advantages of using screw conveyors include their ability to handle a wide range of materials, their flexibility in design, and their ability to operate at various angles and speeds.
What are some disadvantages of using screw conveyors?
Disadvantages of using screw conveyors include their potential for material degradation or damage, their noise level during operation, and their potential for dust generation.
How do screw conveyors compare to other conveying methods, such as belt conveyors or pneumatic conveyors?
Screw conveyors offer advantages over other conveying methods, such as their ability to handle a wider range of materials and their flexibility in design. However, other methods may be more suitable for certain applications, depending on factors such as capacity and operating environment.
What maintenance is required for screw conveyors?
Maintenance for screw conveyors typically includes regular inspections and cleaning, as well as monitoring for wear or damage to components.
What is the lifespan of a screw conveyor?
The lifespan of a screw conveyor depends on various factors, such as the quality of its construction, the materials being conveyed, and the frequency of maintenance and cleaning. A well-maintained screw conveyor can last for many years.
Conclusion:
Screw conveyors are versatile and reliable machines that are widely used in a variety of industries. With their ability to handle a wide range of materials and their flexibility in design, they offer advantages over other conveying methods. However, they do have some disadvantages, such as the potential for material degradation and noise generation. By choosing the right design options and properly maintaining the conveyor, these issues can be minimized. Overall, screw conveyors are an essential tool for transporting materials in a controlled and efficient manner.
Best conveyor systems
In today’s manufacturing industry, the need for efficient and reliable material handling is more critical than ever. Pneumatic conveyors are the go-to solution for manufacturers looking to move materials quickly, cleanly, and safely. These systems are a popular alternative to traditional mechanical conveyors because they provide greater flexibility, reliability, and cost-effectiveness. In this article, we’ll explore the features, advantages, and disadvantages of pneumatic conveyors and answer some frequently asked questions to help you decide if this type of conveyor is right for your manufacturing process.
Features:
- Pneumatic conveyors are highly customizable and can be designed to meet specific material handling needs.
- These conveyors use air pressure to transport materials, making them ideal for moving materials that are sensitive to friction or heat.
- They are available in both positive and negative pressure configurations.
- Positive pressure systems use air to push materials through the conveyor, while negative pressure systems use suction to pull materials through the conveyor.
- Pneumatic conveyors can be used to transport materials over long distances.
- They are commonly used in the food processing, pharmaceutical, and chemical industries.
- These conveyors are easy to clean and sanitize, making them ideal for use in industries with strict cleanliness requirements.
- They are suitable for handling a wide range of materials, including powders, granules, and pellets.
- Pneumatic conveyors are gentle on materials, reducing the risk of material degradation or breakage during transportation.
- They are available in a range of sizes and configurations to suit different material handling needs.
- Pneumatic conveyors are highly efficient, reducing the need for manual labor and increasing productivity.
- They are designed to be low-maintenance, reducing the need for frequent repairs or replacements.
- These conveyors are easy to operate and require minimal training to use.
- They are suitable for use in both indoor and outdoor environments.
- Pneumatic conveyors are highly reliable, with minimal downtime and maximum uptime.
- They are designed to be energy-efficient, reducing operating costs and environmental impact.
- These conveyors can be integrated with other material-handling equipment to create a complete manufacturing solution.
- Pneumatic conveyors can be used to transport materials in hazardous or explosive environments.
- They are suitable for use in high-temperature or low-temperature environments.
- Pneumatic conveyors are available in both portable and stationary configurations.
- These conveyors can be used to transport materials vertically, horizontally, or at an incline.
- They are designed to be easy to maintain, with easy access to critical components for servicing and repair.
- Pneumatic conveyors are highly versatile and can be used for a wide range of applications.
- They are available in both standard and custom designs, allowing manufacturers to choose the right conveyor for their specific needs.
- Pneumatic conveyors are cost-effective, with a low total cost of ownership compared to other material handling solutions.
Advantages:
- Pneumatic conveyors are highly efficient, reducing the need for manual labor and increasing productivity.
- They are gentle on materials, reducing the risk of material degradation or breakage during transportation.
- These conveyors are easy to clean and sanitize, making them ideal for use in industries with strict cleanliness requirements.
- They are suitable for handling a wide range of materials, including powders, granules, and pellets.
- Pneumatic conveyors are highly customizable and can be designed to meet specific material handling needs.
- They are available in a range of sizes and configurations to suit different material handling needs.
- Pneumatic conveyors are easy to operate and require minimal training to use.
- Pneumatic conveyors are designed to be low-maintenance, reducing the need for frequent repairs or replacements.
- These conveyors are suitable for use in both indoor and outdoor environments.
- Pneumatic conveyors are highly reliable, with minimal downtime and maximum uptime.
- They are energy-efficient, reducing operating costs and environmental impact.
- Pneumatic conveyors can be integrated with other material handling equipment to create a complete manufacturing solution.
- They can transport materials in hazardous or explosive environments.
- Pneumatic conveyors can be used to transport materials vertically, horizontally, or at an incline.
- They are cost-effective, with a low total cost of ownership compared to other material handling solutions.
Disadvantages:
- Pneumatic conveyors can be noisy, depending on the material being transported and the system’s design.
- They require a compressed air supply, which can be expensive to operate and maintain.
- Pneumatic conveyors may not be suitable for handling materials that are very heavy or bulky.
- These conveyors may not be ideal for use in applications where precise material control is necessary.
- Pneumatic conveyors may require additional safety features, such as explosion-proof components, to ensure safe operation in hazardous environments.
FAQs & Ans:
What is a pneumatic conveyor?
A pneumatic conveyor is a system that uses air pressure to move materials from one location to another.
What types of materials can be transported using a pneumatic conveyor?
Pneumatic conveyors can transport a wide range of materials, including powders, granules, pellets, and other bulk materials.
How do pneumatic conveyors work?
Pneumatic conveyors use air pressure to move materials through a pipeline or enclosed tube. Positive pressure systems use air to push materials through the conveyor, while negative pressure systems use suction to pull materials through the conveyor.
What are the advantages of using a pneumatic conveyor?
Pneumatic conveyors are highly efficient, gentle on materials, easy to clean, and suitable for a wide range of materials and applications. They are also highly customizable, reliable, and cost-effective.
What industries use pneumatic conveyors?
Pneumatic conveyors are commonly used in the food processing, pharmaceutical, chemical, and plastics industries, among others.
Are pneumatic conveyors safe to use?
Yes, pneumatic conveyors are safe to use when properly designed, installed, and maintained. They may require additional safety features, such as explosion-proof components, when used in hazardous environments.
How do pneumatic conveyors compare to mechanical conveyors?
Pneumatic conveyors are generally more flexible, reliable, and cost-effective than mechanical conveyors. They can also handle a wider range of materials and require less maintenance.
Can pneumatic conveyors be used to transport materials over long distances?
Yes, pneumatic conveyors can be used to transport materials over long distances, making them ideal for applications where materials need to be moved from one location to another.
Are pneumatic conveyors suitable for handling abrasive materials?
Yes, pneumatic conveyors can handle abrasive materials, but the system’s design may need to be modified to minimize wear and damage to the pipeline or enclosed tube.
Can pneumatic conveyors transport materials at high speeds?
Yes, pneumatic conveyors can transport materials at high speeds, making them ideal for applications where speed is important.
How are pneumatic conveyors cleaned and maintained?
Pneumatic conveyors are easy to clean and maintain, with easy access to critical components for servicing and repair. Regular cleaning and maintenance can help ensure the system operates reliably and efficiently
What is the maximum capacity of a pneumatic conveyor?
The maximum capacity of a pneumatic conveyor depends on the specific system’s design, the material being transported, and other factors. However, these systems can handle large volumes of materials, making them ideal for high-volume applications.
Can pneumatic conveyors be used to transport delicate materials?
Yes, pneumatic conveyors are gentle on materials and can be used to transport delicate materials without damaging them.
What is the operating pressure of a pneumatic conveyor?
The operating pressure of a pneumatic conveyor depends on the specific system’s design and the material being transported. However, typical operating pressures range from 5 to 30 psi.
How does a pneumatic conveyor system handle material segregation?
Pneumatic conveyors can minimize material segregation by using controlled airflows to maintain consistent material flow through the system.
Can pneumatic conveyors be used to transport materials at different angles?
Yes, pneumatic conveyors can transport materials at different angles, including vertical and horizontal transport.
How does a pneumatic conveyor system handle materials with different densities?
Pneumatic conveyors can handle materials with different densities by adjusting the system’s air pressure and flow rates to ensure consistent material flow.
How does a pneumatic conveyor system handle materials with different particle sizes?
Pneumatic conveyors can handle materials with different particle sizes by using controlled airflows to maintain consistent material flow through the system.
Can pneumatic conveyors be used in cleanroom environments?
Yes, pneumatic conveyors can be designed for use in cleanroom environments, where maintaining a sterile environment is critical.
What are the key components of a pneumatic conveyor system?
The key components of a pneumatic conveyor system include a material source, a conveying pipeline or enclosed tube, an air compressor, and control equipment.
What factors should be considered when selecting a pneumatic conveyor system?
When selecting a pneumatic conveyor system, factors to consider include the material being transported, the system’s capacity and range, the operating pressure, and the system’s overall design and features.
What are the different types of pneumatic conveyors?
The different types of pneumatic conveyors include dilute phase conveyors, dense phase conveyors, vacuum conveyors, and pressure conveyors.
Can pneumatic conveyors be used to transport materials at different temperatures?
Yes, pneumatic conveyors can be designed to handle materials at different temperatures, making them ideal for a wide range of applications.
What is the maintenance schedule for a pneumatic conveyor system?
The maintenance schedule for a pneumatic conveyor system depends on the specific system’s design and the material being transported. However, regular cleaning and maintenance can help ensure the system operates reliably and efficiently.
How can a pneumatic conveyor system be optimized for maximum efficiency?
A pneumatic conveyor system can be optimized for maximum efficiency by ensuring proper system design, monitoring operating conditions, and regularly cleaning and maintaining the system.
Conclusion:
Pneumatic conveyors are an efficient and reliable material handling solution used in a variety of industries. They offer a wide range of benefits, including gentle material handling, low-maintenance operation, and energy efficiency. While there are some disadvantages to using these systems, they are generally a cost-effective and flexible option for many material handling applications. By understanding the features, advantages, and disadvantages of pneumatic conveyors, companies can make informed decisions about selecting the right material handling solution for their specific needs.
Overhead Conveyors
In today’s fast-paced world, efficiency and productivity are crucial for success in any industry. This is why many businesses are turning to overhead conveyors to streamline their manufacturing and distribution processes. Overhead conveyors are a cost-effective solution for moving products, parts, and materials throughout a facility. In this article, we will discuss the features, advantages, and disadvantages of overhead conveyors, as well as answer some frequently asked questions about them.
Features of Overhead Conveyors
- Customizable: Overhead conveyors can be customized to meet the specific needs of your facility.
- Versatile: They can transport products of various sizes and weights.
- Space-saving: Overhead conveyors take up less floor space compared to traditional conveyors.
- Increases productivity: They can move products faster and more efficiently, resulting in increased productivity.
- Reduced labor costs: Overhead conveyors eliminate the need for manual material handling, reducing labor costs.
- Improved safety: Overhead conveyors reduce the risk of injury to workers by eliminating the need for manual material handling.
- Low maintenance: They require minimal maintenance compared to other types of conveyors.
- Flexibility: Overhead conveyors can be easily reconfigured to accommodate changing production needs.
- Durability: They are built to withstand heavy use and can last for years.
- Energy-efficient: Overhead conveyors use less energy compared to other types of conveyors.
- Low noise: They produce less noise compared to other types of conveyors.
- Speed control: Overhead conveyors can be programmed to move at different speeds.
- Customized load carriers: Load carriers can be designed to fit your specific product needs.
- Overhead storage: Overhead conveyors can also be used for overhead storage, freeing up valuable floor space.
- Automated: Overhead conveyors can be automated, reducing the need for manual labor.
- Gravity-driven: Gravity-driven overhead conveyors can be used to move products downhill without the need for external power.
- Conveyor switches: Conveyor switches can be used to divert products to different locations.
- Temperature-controlled: Overhead conveyors can be designed to operate in high-temperature environments.
- Sanitary: Overhead conveyors can be designed to meet specific sanitary requirements, making them ideal for food and beverage production facilities.
- Low profile: Overhead conveyors have a low profile, making them ideal for facilities with low ceilings.
- Continuous operation: Overhead conveyors can operate continuously, improving production efficiency.
- Modular design: They have a modular design, making them easy to install and expand as needed.
- Cost-effective: Overhead conveyors are a cost-effective solution for material handling.
- Environmentally friendly: They produce less waste compared to other types of conveyors.
- Reduced material damage: Overhead conveyors reduce the risk of product damage during transport.
Advantages of Overhead Conveyors
- Increased productivity: Overhead conveyors can move products faster and more efficiently, resulting in increased productivity.
- Improved safety: Overhead conveyors reduce the risk of injury to workers by eliminating the need for manual material handling.
- Reduced labor costs: Overhead conveyors eliminate the need for manual material handling, reducing labor costs.
- Space-saving: Overhead conveyors take up less floor space compared to traditional conveyors.
- Customizable: Overhead conveyors can be customized to meet the specific needs of your facility.
- Durability: They are built to withstand heavy use and can last for years.
- Low maintenance: They require minimal maintenance compared to other types of conveyors.
- Energy-efficient: Overhead conveyors use less energy compared to other types of conveyors, resulting in cost savings.
- Increased flexibility: Overhead conveyors can be easily reconfigured to accommodate changing production needs.
- Automated operation: Overhead conveyors can be automated, reducing the need for manual labor and increasing efficiency.
- Reduced material handling: Overhead conveyors eliminate the need for manual material handling, reducing the risk of product damage and increasing efficiency.
- Versatility: Overhead conveyors can transport products of various sizes and weights, making them ideal for a wide range of industries.
- Reduced noise levels: Overhead conveyors produce less noise compared to other types of conveyors, creating a quieter and more comfortable work environment.
- Improved product quality: Overhead conveyors reduce the risk of product damage during transport, resulting in higher product quality.
- Reduced environmental impact: Overhead conveyors produce less waste and use less energy compared to other types of conveyors, making them more environmentally friendly.
Disadvantages of Overhead Conveyors
Initial cost: Overhead conveyors can have a higher initial cost compared to other types of conveyors.
Installation: Installation of overhead conveyors can be more complex compared to other types of conveyors, requiring skilled technicians.
Space limitations: Overhead conveyors may not be suitable for facilities with low ceilings or limited space.
Limited load capacity: Overhead conveyors may have a limited load capacity, which may not be suitable for transporting heavy products.
Limited flexibility: Once installed, overhead conveyors may have limited flexibility in terms of their layout and configuration.
FAQs and Answers about Overhead Conveyors
What is an overhead conveyor?
An overhead conveyor is a type of conveyor system that transports products, parts, and materials above ground level.
What industries use overhead conveyors?
Overhead conveyors are used in a wide range of industries, including automotive, food and beverage, manufacturing, and distribution.
What types of products can be transported on overhead conveyors?
Overhead conveyors can transport products of various sizes and weights, including boxes, bags, and pallets.
What are the benefits of using an overhead conveyor?
The benefits of using an overhead conveyor include increased productivity, improved safety, reduced labor costs, space-saving, and reduced material handling.
How does an overhead conveyor work?
An overhead conveyor works by using a track or rail system to transport products above ground level.
Can an overhead conveyor be customized?
Yes, overhead conveyors can be customized to meet the specific needs of your facility.
What is the difference between an overhead conveyor and a traditional conveyor?
An overhead conveyor transports products above ground level, while a traditional conveyor transports products on ground level.
Are overhead conveyors energy-efficient?
Yes, overhead conveyors use less energy compared to other types of conveyors, resulting in cost savings.
Can an overhead conveyor be automated?
Yes, overhead conveyors can be automated, reducing the need for manual labor and increasing efficiency.
What types of load carriers can be used with overhead conveyors?
Load carriers can be designed to fit your specific product needs, including hooks, trolleys, and trays.
How long does an overhead conveyor last?
Overhead conveyors are built to withstand heavy use and can last for years with proper maintenance.
How much maintenance does an overhead conveyor require?
Overhead conveyors require minimal maintenance compared to other types of conveyors.
What are some safety features of an overhead conveyor?
Safety features of an overhead conveyor may include emergency stop buttons, safety gates, and warning signals.
Can an overhead conveyor be used for overhead storage?
Yes, overhead conveyors can also be used for overhead storage
What is the maximum weight that an overhead conveyor can carry?
The maximum weight that an overhead conveyor can carry depends on the specific model and design, but they can typically handle loads up to several hundred pounds.
Can an overhead conveyor be used in a cleanroom environment?
Yes, overhead conveyors can be designed to meet cleanroom requirements, including stainless steel construction and air filtration systems.
How does an overhead conveyor handle curves and turns?
Overhead conveyors can be designed with curves and turn to accommodate the layout of your facility.
Can an overhead conveyor be used for assembly line production?
Yes, overhead conveyors are commonly used for assembly line production, as they allow products to move through various stages of production without being touched by workers.
What is the maintenance schedule for an overhead conveyor?
The maintenance schedule for an overhead conveyor will depend on the specific model and usage, but it typically involves regular cleaning, lubrication, and inspection.
How long does it take to install an overhead conveyor?
The installation time for an overhead conveyor will depend on the specific model and design, as well as the layout of your facility.
Can an overhead conveyor be used for outdoor applications?
Yes, overhead conveyors can be designed for outdoor use, with features such as weather-resistant materials and protective covers.
What is the cost of an overhead conveyor?
The cost of an overhead conveyor will depend on the specific model, design, and installation requirements. They can range from several thousand to tens of thousands of dollars.
Can an overhead conveyor be integrated with other automation systems?
Yes, overhead conveyors can be integrated with other automation systems, such as robotics and sorting systems.
How does an overhead conveyor improve safety?
Overhead conveyors improve safety by reducing the need for manual material handling and reducing the risk of worker injury and product damage.
How does an overhead conveyor save space?
Overhead conveyors save space by transporting products above ground level, eliminating the need for floor space that traditional conveyors require.
Conclusion
Overhead conveyors are a versatile and efficient solution for transporting products and materials in various industries. They offer numerous benefits, including increased productivity, improved safety, reduced labor costs, and space-saving. While they may have a higher initial cost and require skilled installation, their long lifespan, and minimal maintenance make them a cost-effective choice in the long run. With their customizable design and ability to handle various product sizes and weights, overhead conveyors are a valuable addition to any facility looking to improve their material handling processes.
Vibrating Conveyors
Vibrating conveyors are widely used in manufacturing and material handling industries. They offer an efficient and effective way to move materials, such as bulk solids and powders, from one location to another. Vibrating conveyors use vibrations to move materials, which means they are quieter and more energy efficient than traditional belt conveyors.
In this article, we will explore the features, advantages, and disadvantages of vibrating conveyors. We will also answer frequently asked questions about these conveyors to help you understand their use and applications.
Features of Vibrating Conveyors:
- Vibrating conveyors are compact and can fit into small spaces.
- They are easy to install and maintain.
- Vibrating conveyors can handle a wide range of materials, including fragile and abrasive materials.
- They are quieter than other types of conveyors.
- Vibrating conveyors have a low operating cost.
- They are energy-efficient, using less power than traditional conveyors.
- Vibrating conveyors can handle high temperatures and harsh environments.
- They have a low profile, making them ideal for applications with limited headroom.
- Vibrating conveyors can be customized to meet specific requirements.
- They have a simple design, making them easy to troubleshoot and repair.
- Vibrating conveyors can handle both horizontal and vertical conveying.
- They offer continuous conveying without the need for stopping and starting.
- Vibrating conveyors are suitable for conveying materials over long distances.
- They can be used for both bulk material handling and packaging applications.
- Vibrating conveyors can be used for both dry and wet materials.
- They are gentle on materials, reducing the risk of product damage.
- Vibrating conveyors can be used to convey materials at high speeds.
- They can be used in conjunction with other equipment, such as scales and feeders.
- Vibrating conveyors can be designed to meet specific hygiene standards for food and pharmaceutical applications.
- They can be used in hazardous environments, such as explosive or flammable atmospheres.
- Vibrating conveyors can be used in both manual and automated systems.
- They have a low maintenance requirement.
- Vibrating conveyors are easy to clean and sanitize.
- They have a long service life.
- Vibrating conveyors are available in a range of sizes and capacities.
Advantages of Vibrating Conveyors:
- Vibrating conveyors offer an efficient and effective way to move materials.
- They are quieter and more energy efficient than traditional conveyors.
- Vibrating conveyors can handle a wide range of materials, including fragile and abrasive materials.
- They have a low operating cost.
- Vibrating conveyors can handle high temperatures and harsh environments.
- They have a low profile, making them ideal for applications with limited headroom.
- Vibrating conveyors can be customized to meet specific requirements.
- They offer continuous conveying without the need for stopping and starting.
- Vibrating conveyors are suitable for conveying materials over long distances.
- They can be used for both bulk material handling and packaging applications.
- Vibrating conveyors can be used for both dry and wet materials.
- They are gentle on materials, reducing the risk of product damage.
- Vibrating conveyors can be used to convey materials at high speeds.
- They can be used in hazardous environments, such as explosive or flammable atmospheres.
- Vibrating conveyors have a long service life.
Disadvantages of Vibrating Conveyors:
- Vibrating conveyors can be noisy if not properly designed and maintained.
- They may require more frequent maintenance than traditional conveyors.
- Vibrating conveyors may require more frequent cleaning than traditional conveyors.
- They may not be suitable for all types of materials, such as materials that are extremely heavy or have a high moisture content.
- Vibrating conveyors may require more initial investment than traditional conveyors.
FAQs & Ans:
What types of materials can be conveyed using vibrating conveyors?
Ans: Vibrating conveyors can handle a wide range of materials, including bulk solids, powders, granules, and fragile materials.
Can vibrating conveyors be used to convey wet materials?
Ans: Yes, vibrating conveyors can be used to convey both dry and wet materials.
What is the maximum distance that vibrating conveyors can convey materials?
Ans: Vibrating conveyors can be used to convey materials over long distances, depending on the specific application and design.
Can vibrating conveyors be used in explosive or flammable environments?
Ans: Yes, vibrating conveyors can be designed for use in hazardous environments, such as explosive or flammable atmospheres.
How energy-efficient are vibrating conveyors compared to traditional conveyors?
Ans: Vibrating conveyors are more energy-efficient than traditional conveyors because they use vibrations to move materials, which requires less power.
Are vibrating conveyors noisy?
Ans: Vibrating conveyors can be noisy if not properly designed and maintained, but they are generally quieter than traditional conveyors.
How can I maintain my vibrating conveyor?
Ans: Vibrating conveyors are easy to maintain and can be cleaned and sanitized easily. Regular inspection and lubrication are important for ensuring optimal performance.
Can vibrating conveyors be used for food handling?
Ans: Yes, vibrating conveyors can be designed to meet specific hygiene standards for food and pharmaceutical applications.
What is the maximum weight that vibrating conveyors can handle?
Ans: The weight capacity of vibrating conveyors depends on the specific design and application, but they can handle a wide range of weights.
Can vibrating conveyors be used for packaging applications?
Ans: Yes, vibrating conveyors can be used for both bulk material handling and packaging applications.
How do vibrating conveyors compare to traditional belt conveyors?
Ans: Vibrating conveyors are quieter, more energy-efficient, and more versatile than traditional belt conveyors.
What is the difference between horizontal and vertical vibrating conveyors?
Ans: Horizontal vibrating conveyors move materials horizontally, while vertical vibrating conveyors move materials vertically.
Are there any safety concerns when using vibrating conveyors?
Ans: Safety concerns when using vibrating conveyors include the risk of materials becoming stuck or jammed, as well as the risk of vibration-induced fatigue.
Can vibrating conveyors be used to convey materials at high speeds?
Ans: Yes, vibrating conveyors can be used to convey materials at high speeds, making them ideal for high-volume applications.
How customizable are vibrating conveyors?
Ans: Vibrating conveyors can be customized to meet specific requirements, including size, capacity, and material handling needs.
What is the typical lifespan of a vibrating conveyor?
Ans: The lifespan of a vibrating conveyor depends on the specific design, materials, and application, but they generally have a long service life.
How do I troubleshoot my vibrating conveyor?
Ans: Common troubleshooting steps for vibrating conveyors include inspecting the drive motor, checking for blockages, and adjusting the conveyor’s speed.
Are vibrating conveyors suitable for outdoor use?
Ans: Vibrating conveyors can be used in both indoor and outdoor environments, but they may require additional protection against the elements in outdoor applications.
Can vibrating conveyors be used in automated systems?
Ans: Yes, vibrating conveyors can be used in both manual and automated systems and can be integrated with other equipment to create a complete material handling system.
What is the maintenance schedule for vibrating conveyors?
Ans: The maintenance schedule for vibrating conveyors will vary depending on the specific design and application, but regular inspection and lubrication are typically recommended.
What is the difference between a vibrating conveyor and a vibratory feeder?
Ans: A vibrating conveyor is used for transporting materials from one location to another, while a vibratory feeder is used for metering and controlling the flow of materials.
Can vibrating conveyors be used for sorting and screening applications?
Ans: Yes, vibrating conveyors can be used for sorting and screening applications, depending on the specific design and application.
How do I choose the right vibrating conveyor for my application?
Ans: When choosing a vibrating conveyor, consider the specific requirements of your application, including material type, capacity, and handling needs.
What safety precautions should I take when operating a vibrating conveyor?
Ans: Safety precautions when operating a vibrating conveyor include wearing appropriate personal protective equipment and ensuring that all guards and safety features are in place and functioning properly.
Can vibrating conveyors be used in cleanroom environments?
Ans: Yes, vibrating conveyors can be designed to meet specific hygiene standards for cleanroom applications, such as in the pharmaceutical or semiconductor industries.
Conclusion:
Vibrating conveyors are versatile and efficient material handling solutions that can be customized to meet specific application requirements. They offer a range of advantages, including energy efficiency, versatility, and ease of maintenance. However, they may not be suitable for all types of materials and may require more frequent cleaning than traditional conveyors. Overall, vibrating conveyors are an excellent choice for applications that require efficient and reliable material handling.
Bucket Conveyors
Bucket conveyors are industrial machines that are used for transporting bulk materials in large quantities vertically, typically in industries such as agriculture, mining, and construction. Bucket conveyors are also known as bucket elevators or bucket lifts. They are designed to move materials in a continuous manner by using a series of buckets attached to a chain or belt that rotates around two or more pulleys or sprockets. This article will explore the features, advantages, disadvantages, FAQs, and conclusions of bucket conveyors.
Features of Bucket Conveyors:
- Bucket conveyors are designed for handling a wide range of materials, including granular, powders, and lumpy materials.
- They are used for the vertical transportation of materials, from one level to another.
- Bucket conveyors can handle materials at high speeds, making them ideal for high-volume production environments.
- They are available in different sizes, capacities, and designs to meet specific application needs.
- Bucket conveyors can be customized to meet the unique requirements of different industries.
- They are easy to install, operate, and maintain.
- Bucket conveyors are durable and built to last, making them a reliable choice for industries with heavy-duty applications.
- They can be constructed from a variety of materials, including stainless steel, carbon steel, and aluminum.
- Bucket conveyors can be fitted with a range of features, such as sensors, control systems, and safety devices.
- They are suitable for use in hazardous environments, as they can be fitted with explosion-proof components.
- Bucket conveyors can be used for both indoor and outdoor applications.
- They are designed to handle a variety of temperatures, from high to low.
- Bucket conveyors are low-maintenance and have a long service life.
- They are energy-efficient and have low operating costs.
- Bucket conveyors can be used to transport materials over long distances.
- They can handle materials with a wide range of densities and sizes.
- Bucket conveyors are easy to clean and sanitize, making them ideal for food and beverage processing.
- They are capable of transporting materials in a gentle and controlled manner, which helps prevent damage to delicate materials.
- Bucket conveyors are ideal for transporting materials that are prone to segregation.
- They can be used in conjunction with other equipment, such as storage silos and processing equipment.
- Bucket conveyors are suitable for both continuous and intermittent operations.
- They are versatile and can be used for a variety of applications, including conveying, loading, and unloading.
- Bucket conveyors are designed for ease of maintenance, with easy access to key components for inspection and cleaning.
- They are customizable to fit specific applications, including those with limited space or difficult access.
- Bucket conveyors can be operated automatically, reducing the need for manual labor.
Advantages of Bucket Conveyors:
- Bucket conveyors are designed to move materials vertically, which is useful for industries with limited floor space.
- They can handle a wide range of materials, making them versatile and useful in many different applications.
- Bucket conveyors are efficient and can transport materials quickly and smoothly, improving production rates.
- They can be customized to meet the specific needs of different industries and applications.
- Bucket conveyors are low-maintenance and have a long service life, reducing downtime and maintenance costs.
- They are energy-efficient and have low operating costs, making them cost-effective for businesses.
- Bucket conveyors are designed for ease of cleaning and sanitization, making them ideal for food and beverage processing.
- They can handle materials gently and carefully, which is important for industries that deal with fragile materials.
- Bucket conveyors can be operated automatically They are safe to use, as they can be fitted with safety devices and sensors to prevent accidents and injuries.
- Bucket conveyors are suitable for use in hazardous environments, as they can be fitted with explosion-proof components.
- They can be used in conjunction with other equipment, such as storage silos and processing equipment, to create a complete material handling system.
- Bucket conveyors are versatile and can be used for a variety of applications, including conveying, loading, and unloading.
- They are easy to install, operate, and maintain, reducing the need for specialized training and expertise.
- Bucket conveyors are a reliable choice for industries with heavy-duty applications, as they are built to last and can withstand harsh environments.
Disadvantages of Bucket Conveyors:
- Bucket conveyors can be noisy, which can be a concern for workers and neighboring businesses.
- They can be expensive to purchase and install, particularly for businesses with limited budgets.
- Bucket conveyors may not be suitable for handling certain materials, such as materials that are sticky or prone to clumping.
- They can require a significant amount of maintenance to keep them running smoothly, particularly if they are used frequently.
- Bucket conveyors can be challenging to clean, particularly if they are used to transport materials that are prone to sticking or staining.
FAQs and Answers about Bucket Conveyors:
What materials can be transported using bucket conveyors?
Bucket conveyors can handle a wide range of materials, including granular, powders, and lumpy materials.
How are bucket conveyors powered?
Bucket conveyors are typically powered by an electric motor, which drives a chain or belt that moves the buckets.
What industries use bucket conveyors?
Bucket conveyors are commonly used in industries such as agriculture, mining, construction, and food and beverage processing.
Can bucket conveyors be customized to fit specific applications?
Yes, bucket conveyors can be customized to meet the unique requirements of different industries and applications.
Are bucket conveyors easy to install?
Yes, bucket conveyors are typically easy to install, with many manufacturers providing detailed instructions and support.
How do bucket conveyors compare to other types of conveyors?
Bucket conveyors are designed for the vertical transportation of materials, making them useful for industries with limited floor space. They can handle a wide range of materials and are efficient, cost-effective, and reliable.
Are bucket conveyors energy-efficient?
Yes, bucket conveyors are energy-efficient and have low operating costs, making them a cost-effective choice for businesses.
Can bucket conveyors be used for hazardous materials?
Yes, bucket conveyors can be fitted with explosion-proof components and used in hazardous environments.
How do bucket conveyors handle delicate materials?
Bucket conveyors can handle materials gently and carefully, which is important for industries that deal with fragile materials.
Can bucket conveyors be used outdoors?
Yes, bucket conveyors can be used for both indoor and outdoor applications.
How are bucket conveyors maintained?
Bucket conveyors are typically low-maintenance and have a long service life. They require regular cleaning and inspection to keep them running smoothly.
Are bucket conveyors noisy?
Yes, bucket conveyors can be noisy, particularly if they are used in a noisy environment.
How do bucket conveyors handle materials that are prone to segregation?
Bucket conveyors are ideal for transporting materials that are prone to segregation, as the buckets are designed to keep the materials separate and prevent mixing.
Can bucket conveyors be used for continuous operations?
Yes, bucket conveyors are suitable for both continuous and intermittent operations.
Are bucket conveyors customizable?
Yes, bucket conveyors can be customized to fit specific requirements, such as the material being transported, the height and distance of the transportation, and the desired speed.
What is the maximum capacity of a bucket conveyor?
The maximum capacity of a bucket conveyor depends on various factors, including the size and shape of the buckets, the speed of the conveyor, and the type of material being transported.
Can bucket conveyors be used for high-temperature materials?
Yes, bucket conveyors can be designed to handle high-temperature materials, with specialized components and materials.
How do bucket conveyors prevent material loss?
Bucket conveyors are designed with a tight seal to prevent material loss during transportation.
How do bucket conveyors handle materials with different densities?
Bucket conveyors can handle materials with different densities, as the buckets are designed to carry a fixed volume of material, regardless of its density.
Are bucket conveyors suitable for long-distance transportation?
Yes, bucket conveyors can be used for long-distance transportation, with multiple conveyors linked together to transport materials over a long distance.
How do bucket conveyors handle materials with different particle sizes?
Bucket conveyors can handle materials with different particle sizes, as the buckets can be designed to accommodate different sizes and shapes of material.
Can bucket conveyors be used for the vertical transportation of liquids?
Bucket conveyors are not suitable for the vertical transportation of liquids, as the buckets are not designed to handle fluids.
Can bucket conveyors be used for inclined transportation?
Yes, bucket conveyors can be used for inclined transportation, with specialized components and designs to prevent spillage and material loss.
What is the maximum height at that a bucket conveyor can transport materials?
The maximum height that a bucket conveyor can transport materials depends on various factors, including the size and shape of the buckets, the speed of the conveyor, and the type of material being transported.
Can bucket conveyors be used in corrosive environments?
Bucket conveyors can be designed to withstand corrosive environments, with specialized coatings and materials.
Conclusion:
In conclusion, bucket conveyors are a versatile and reliable solution for material handling in various industries. With their ability to handle a wide range of materials, customized designs, and low operating costs, bucket conveyors are a popular choice for businesses looking to streamline their material handling processes. While they do have some disadvantages, such as noise and maintenance requirements, the benefits far outweigh the drawbacks. Whether used for conveying, loading, or unloading, bucket conveyors are an efficient and cost-effective solution that can help businesses increase productivity and profitability.
Magnetic Conveyors
Conveyors are an essential part of any manufacturing or industrial process. They are used to transport materials and products from one place to another. The latest addition to this field is magnetic conveyors. They use magnetic forces to move materials, making them a versatile and efficient solution for a wide range of industries. In this article, we will discuss 25 features, 15 advantages, 5 disadvantages, 30 FAQs & Ans, and conclude with why magnetic conveyors are the future of material handling.
Features:
- Magnetic conveyors use permanent magnets to move materials instead of traditional belts or rollers.
- They are ideal for transporting delicate or fragile materials that can be damaged by traditional conveyor belts.
- Magnetic conveyors are energy-efficient and require less power to operate.
- They are easy to install and can be customized to meet specific requirements.
- Magnetic conveyors are low maintenance and do not require frequent replacement of parts.
- They are capable of moving materials in any direction, including uphill or downhill.
- Magnetic conveyors are ideal for transporting materials over long distances.
- They are designed to operate quietly, making them suitable for use in environments where noise levels must be kept to a minimum.
- Magnetic conveyors are versatile and can be used to transport a wide range of materials, including ferrous and non-ferrous metals, plastics, and food products.
- They are suitable for use in both wet and dry environments.
- Magnetic conveyors can be operated manually or automatically, depending on the needs of the application.
- They are designed to be durable and can withstand harsh environments.
- Magnetic conveyors are safe to operate, with no risk of injury from moving parts.
- They are ideal for use in applications where hygiene is important, such as in the food and pharmaceutical industries.
- Magnetic conveyors are available in various sizes and configurations to meet specific application requirements.
- They can be used in combination with other best conveyor systems, such as belt conveyors or gravity conveyors, to create a complete material handling solution.
- Magnetic conveyors are easy to clean and maintain, with no need for lubrication.
- They are highly efficient, with a low cost of ownership and a long service life.
- Magnetic conveyors are environmentally friendly, with no emissions or pollutants.
- They are designed to be flexible and can be easily modified to accommodate changes in production requirements.
- Magnetic conveyors are reliable and have a high uptime, ensuring that materials are transported efficiently and without interruption.
- They are designed to be safe and easy to operate, with no special training required.
- Magnetic conveyors are suitable for use in hazardous environments, such as in the chemical and petrochemical industries.
- They are capable of handling heavy loads, making them ideal for use in industries such as mining and construction.
- Magnetic conveyors are a cost-effective solution for material handling, with a low total cost of ownership compared to other best conveyor systems.
Advantages:
- Magnetic conveyors are more energy-efficient than traditional best conveyor systems, reducing operating costs and environmental impact.
- They are capable of moving materials in any direction, providing greater flexibility in the design of material handling systems.
- Magnetic conveyors are suitable for transporting delicate or fragile materials that can be damaged by traditional conveyor belts.
- They are easy to install and require minimal maintenance, reducing downtime and maintenance costs.
- Magnetic conveyors are highly reliable, with long service life and high uptime.
- They are environmentally friendly, with no emissions or pollutants.
- Magnetic conveyors are safe to operate, with no risk of injury from moving parts.
- They are suitable for use in a wide range of industries, including food, pharmaceutical
- Magnetic conveyors are ideal for use in hazardous environments, such as those found in the chemical and petrochemical industries.
- They are designed to be flexible and can be easily modified to accommodate changes in production requirements.
- Magnetic conveyors are available in various sizes and configurations, allowing them to be tailored to specific application requirements.
- They are capable of handling heavy loads, making them suitable for use in the mining and construction industries.
- Magnetic conveyors are designed to be hygienic and easy to clean, making them suitable for use in the food and pharmaceutical industries.
- They are ideal for use in applications where noise levels must be kept to a minimum, such as in hospitals and research facilities.
- Magnetic conveyors have a low cost of ownership, making them a cost-effective solution for material handling.
Disadvantages:
- Magnetic conveyors may not be suitable for handling materials that are not attracted to magnets.
- They may require additional support structures to prevent sagging and ensure proper alignment.
- Magnetic conveyors may require more frequent cleaning than traditional best conveyor systems to maintain their efficiency.
- They may be more expensive to purchase upfront compared to traditional best conveyor systems.
- Magnetic conveyors require specialized expertise for design, installation, and maintenance.
FAQs & Ans:
What materials can be transported using magnetic conveyors?
Magnetic conveyors are suitable for a wide range of materials, including ferrous and non-ferrous metals, plastics, and food products.
How do magnetic conveyors work?
Magnetic conveyors use permanent magnets to create a magnetic field that attracts and moves materials along the conveyor.
Are magnetic conveyors suitable for use in wet environments?
Yes, magnetic conveyors are suitable for use in both wet and dry environments.
Can magnetic conveyors be used to transport materials over long distances?
Yes, magnetic conveyors are ideal for transporting materials over long distances.
Are magnetic conveyors energy-efficient?
Yes, magnetic conveyors are more energy-efficient than traditional best conveyor systems.
Are magnetic conveyors easy to install?
Yes, magnetic conveyors are easy to install and can be customized to meet specific requirements.
How often do magnetic conveyors require maintenance?
Magnetic conveyors are low maintenance and do not require frequent replacement of parts.
Can magnetic conveyors be used to transport delicate materials?
Yes, magnetic conveyors are ideal for transporting delicate or fragile materials that can be damaged by traditional conveyor belts.
Are magnetic conveyors suitable for use in hazardous environments?
Yes, magnetic conveyors are suitable for use in hazardous environments, such as those found in the chemical and petrochemical industries.
Are magnetic conveyors safe to operate?
Yes, magnetic conveyors are safe to operate, with no risk of injury from moving parts.
Do magnetic conveyors produce noise during operation?
No, magnetic conveyors are designed to operate quietly, making them suitable for use in environments where noise levels must be kept to a minimum.
Are magnetic conveyors environmentally friendly?
Yes, magnetic conveyors are environmentally friendly, with no emissions or pollutants.
Can magnetic conveyors be used in combination with other best conveyor systems?
Yes, magnetic conveyors can be used in combination with other best conveyor systems, such as belt conveyors or gravity conveyors, to create a complete material handling solution.
Can magnetic conveyors handle heavy loads?
Yes, magnetic conveyors are capable of handling heavy loads, making them suitable for use in industries such as mining and construction.
Are magnetic conveyors suitable for use in the food industry?
Yes, magnetic conveyors are ideal for use in the food industry, where hygiene is important.
How do you clean a magnetic conveyor?
Magnetic conveyors are easy to clean and can be cleaned using a variety of methods, including steam cleaning, pressure washing, or wiping with a damp cloth.
Are magnetic conveyors suitable for use with corrosive materials?
Yes, magnetic conveyors can be designed to handle corrosive materials, with appropriate materials and coatings used in their construction.
Are magnetic conveyors customizable?
Yes, magnetic conveyors are highly customizable and can be tailored to meet specific application requirements.
Can magnetic conveyors be used to sort materials?
Yes, magnetic conveyors can be used for material sorting, with the magnetic field used to separate materials based on their magnetic properties.
Are magnetic conveyors suitable for use in high-temperature environments?
Yes, magnetic conveyors can be designed to withstand high temperatures, with appropriate materials and cooling systems used in their construction.
How do you maintain a magnetic conveyor?
Magnetic conveyors require minimal maintenance, with periodic cleaning and inspection recommended to ensure efficient operation.
Can magnetic conveyors be used in vertical applications?
Yes, magnetic conveyors can be used in vertical applications, with appropriate modifications made to their design.
How do you control the speed of a magnetic conveyor?
The speed of a magnetic conveyor can be controlled using a variable frequency drive (VFD) or other speed control system.
Are magnetic conveyors suitable for use with abrasive materials?
Yes, magnetic conveyors can be designed to handle abrasive materials, with appropriate materials and coatings used in their construction.
How do you choose the right magnetic conveyor for your application?
Choosing the right magnetic conveyor depends on a variety of factors, including the type and size of material being transported, the required throughput rate, and the specific application requirements.
Conclusion:
Magnetic conveyors are a versatile and efficient solution for material handling applications. With their ability to transport a wide range of materials, low maintenance requirements, and customizable design options, they offer many advantages over traditional conveyor systems. While there are some limitations and considerations to keep in mind, such as their higher upfront cost and specialized expertise required for installation and maintenance, the benefits of magnetic conveyors make them a worthwhile investment for many industries. Whether you are in the food, pharmaceutical, mining, or construction industry, magnetic conveyors offer a reliable and efficient way to move your materials from point A to point B.
Spiral Conveyors
Spiral conveyors are a type of mechanical conveyor system that is used to move materials vertically or horizontally in a continuous, spiral motion. They are a versatile and efficient solution for handling a wide range of materials, including food, pharmaceuticals, chemicals, and more. Spiral conveyors are used in a variety of industries, including manufacturing, distribution, and warehousing.
In this article, we will explore the features, advantages, and disadvantages of spiral conveyors. We will also address some frequently asked questions about these conveyor systems.
Features of Spiral Conveyors:
- Vertical and horizontal transport: Spiral conveyors can transport materials both vertically and horizontally.
- Space-saving: Spiral conveyors take up less floor space than traditional conveyor systems.
- Customizable: Spiral conveyors can be customized to fit the specific needs of the application.
- Modular design: Spiral conveyors are designed in modules, making it easy to add or remove sections as needed.
- Easy maintenance: Spiral conveyors are designed for easy maintenance and cleaning.
- Gentle handling: Spiral conveyors provide gentle handling of materials, reducing the risk of damage.
- High throughput: Spiral conveyors have a high throughput capacity, making them ideal for high-volume applications.
- Energy-efficient: Spiral conveyors are energy-efficient, helping to reduce operating costs.
- Low noise: Spiral conveyors operate quietly, making them suitable for use in noise-sensitive environments.
- Safe: Spiral conveyors are designed with safety in mind, with features such as guardrails and emergency stop buttons.
- Flexible: Spiral conveyors are flexible, allowing them to handle a wide range of materials and applications.
- Continuous operation: Spiral conveyors can operate continuously, providing a steady flow of materials.
- Variable speed: Spiral conveyors can operate at variable speeds, allowing for greater control over the material flow.
- Durable: Spiral conveyors are built to last, with robust construction and high-quality materials.
- Low maintenance: Spiral conveyors require minimal maintenance, helping to reduce downtime and operating costs.
- Easy to install: Spiral conveyors are easy to install, with minimal disruption to operations.
- Hygienic: Spiral conveyors are designed for hygienic operation, with features such as easy-to-clean surfaces and food-grade materials.
- Non-corrosive: Spiral conveyors are resistant to corrosion, making them suitable for use in harsh environments.
- Low profile: Spiral conveyors have a low profile, making them ideal for use in confined spaces.
- Accurate positioning: Spiral conveyors provide accurate positioning of materials, ensuring precise placement.
- Low vibration: Spiral conveyors operate with low vibration, reducing wear and tear on machinery and equipment.
- Adjustable incline: Spiral conveyors can be adjusted to change the incline, allowing for greater control over the material flow.
- Minimal product degradation: Spiral conveyors minimize product degradation, ensuring that materials arrive at their destination in the same condition as when they were loaded.
- Low installation costs: Spiral conveyors have lower installation costs than traditional conveyor systems.
- Reduces labor costs: Spiral conveyors reduce labor costs by automating the transport of materials.
Advantages of Spiral Conveyors:
- Increased efficiency: Spiral conveyors increase efficiency by reducing the time and labor required to transport materials.
- Improved safety: Spiral conveyors improve safety by reducing the risk of accidents and injuries.
- Lower operating costs: Spiral conveyors have lower operating costs than traditional conveyor systems, thanks to their energy efficiency and low maintenance requirements.
- Greater throughput: Spiral conveyors have a higher throughput capacity than traditional conveyor systems, allowing for faster material transport.
- Improved accuracy: Spiral conveyors improve accuracy by providing precise positioning of materials, reducing the risk of errors.
- Increased productivity: Spiral conveyors increase productivity by automating the transport of materials, allowing workers to focus on other tasks.
- Reduced product damage: Spiral conveyors provide gentle handling of materials, reducing the risk of damage during transport.
- Versatile: Spiral conveyors are versatile and can handle a wide range of materials, making them suitable for a variety of applications.
- Space-saving: Spiral conveyors take up less space than traditional conveyor systems, making them ideal for applications where space is limited.
- Improved hygiene: Spiral conveyors are designed for hygienic operation, reducing the risk of contamination in food and pharmaceutical applications.
- Reduced environmental impact: Spiral conveyors are energy-efficient, reducing the environmental impact of material transport.
- Increased flexibility: Spiral conveyors are flexible and can be customized to fit the specific needs of the application, allowing for greater control over the material flow.
- Reduced labor costs: Spiral conveyors reduce labor costs by automating the transport of materials, reducing the need for manual labor.
- Improved ergonomics: Spiral conveyors improve ergonomics by reducing the physical strain of manual material transport.
- Reduced maintenance costs: Spiral conveyors have lower maintenance costs than traditional conveyor systems, reducing downtime and repair costs.
Disadvantages of Spiral Conveyors:
Higher initial cost: Spiral conveyors have a higher initial cost than traditional conveyor systems.
Limited to certain materials: Spiral conveyors may not be suitable for certain materials, such as those that are fragile or prone to sticking together.
Limited throughput capacity: Spiral conveyors have a limited throughput capacity compared to other types of conveyor systems.
More complex design: Spiral conveyors have a more complex design than traditional conveyor systems, making them more difficult to install and maintain.
Limited flexibility: Spiral conveyors may not be as flexible as other types of conveyor systems, making them less suitable for certain applications.
FAQs & Ans:
What materials can be transported on a spiral conveyor?
Answer: Spiral conveyors can handle a wide range of materials, including food, pharmaceuticals, chemicals, and more.
How does a spiral conveyor work?
Answer: Spiral conveyors use a continuous spiral motion to transport materials vertically or horizontally.
What are the benefits of a spiral conveyor?
Answer: Spiral conveyors provide benefits such as increased efficiency, improved safety, lower operating costs, and more.
What industries use spiral conveyors?
Answer: Spiral conveyors are used in a variety of industries, including manufacturing, distribution, and warehousing.
Can spiral conveyors be customized?
Answer: Yes, spiral conveyors can be customized to fit the specific needs of the application.
Are spiral conveyors energy-efficient?
Answer: Yes, spiral conveyors are energy-efficient, helping to reduce operating costs.
How much space do spiral conveyors take up?
Answer: Spiral conveyors take up less floor space than traditional conveyor systems.
Are spiral conveyors easy to install?
Answer: Yes, spiral conveyors are easy to install, with minimal disruption to operations.
Can spiral conveyors handle fragile materials?
Answer: Spiral conveyors may not be suitable for certain fragile materials, as they can be damaged during transport.
What is the maintenance requirement for a spiral conveyor?
Answer: Spiral conveyors require minimal maintenance, helping to reduce downtime and operating costs.
Are spiral conveyors suitable for food applications?
Answer: Yes, spiral conveyors are designed for hygienic operation and are suitable for food applications.
How does a spiral conveyor reduce labor costs?
Answer: Spiral conveyors reduce labor costs by automating the transport of materials, reducing the need for manual labor.
What is the throughput capacity of a spiral conveyor?
Answer: The throughput capacity of a spiral conveyor can vary depending on the specific model and application.
Can spiral conveyors be used for vertical transport?
Answer: Yes, spiral conveyors can be used for both vertical and horizontal transport.
How do spiral conveyors compare to other types of conveyor systems?
Answer: Spiral conveyors offer benefits such as increased efficiency, improved safety, and reduced operating costs compared to other types of conveyor systems.
What are some common applications for spiral conveyors?
Answer: Some common applications for spiral conveyors include packaging and distribution, food and beverage processing, and pharmaceutical manufacturing.
What are some design considerations for a spiral conveyor?
Answer: Some design considerations for a spiral conveyor include material type, throughput capacity, space requirements, and hygienic design.
Can spiral conveyors be integrated with other conveyor systems?
Answer: Yes, spiral conveyors can be integrated with other conveyor systems for seamless material handling.
How do you choose the right spiral conveyor for your application?
Answer: To choose the right spiral conveyor, consider factors such as material type, throughput capacity, space requirements, and budget.
Are spiral conveyors suitable for heavy-duty applications?
Answer: Yes, spiral conveyors can be designed for heavy-duty applications, with higher load capacities and more durable construction.
Can spiral conveyors handle both small and large materials?
Answer: Yes, spiral conveyors can handle both small and large materials, with customizable chute sizes and spiral pitch.
How do spiral conveyors improve safety?
Answer: Spiral conveyors improve safety by reducing the risk of manual material handling injuries and providing precise positioning of materials.
Can spiral conveyors be used in high-speed applications?
Answer: Yes, spiral conveyors can be designed for high-speed applications, with faster spiral rotations and optimized chute designs.
How do spiral conveyors reduce product damage?
Answer: Spiral conveyors provide gentle handling of materials, reducing the risk of damage during transport.
What is the lead time for a spiral conveyor?
Answer: The lead time for a spiral conveyor can vary depending on the specific model and customization options.
Conclusion:
In conclusion, spiral conveyors offer a range of benefits for material handling applications, including increased efficiency, improved safety, and reduced operating costs. With customizable options for material type, throughput capacity, and space requirements, spiral conveyors can be tailored to fit the specific needs of a wide range of industries. While there are some disadvantages, such as higher initial costs and limited throughput capacity, the advantages of spiral conveyors make them a valuable investment for companies looking to optimize their material handling processes.
Features
Customizable: Conveyor systems can be customized to fit specific needs and requirements.
Efficiency: Conveyor systems can increase efficiency and productivity by automating the movement of materials.
Versatility: Conveyor systems can be used to transport a wide range of products and materials.
Safety: Conveyor systems can improve safety by reducing the need for manual handling of materials.
Durability: Conveyor systems are built to withstand harsh environments and heavy use.
Speed: Conveyor systems can move materials quickly and efficiently, increasing production speed.
Integration: Conveyor systems can be integrated with other equipment such as robots and sensors to create a fully automated system.
Space-saving: Conveyor systems can be designed to fit into small spaces, maximizing floor space.
Low maintenance: Conveyor systems require minimal maintenance and can operate for long periods of time without interruption.
Cost-effective: Conveyor systems can be a cost-effective solution for material handling, reducing labor costs and increasing efficiency.
Energy-efficient: Conveyor systems can be designed to be energy-efficient, reducing energy costs.
Scalable: Conveyor systems can be easily scaled up or down to meet changing needs and requirements.
Consistency: Conveyor systems can ensure consistency in the movement of materials, reducing errors and improving quality control.
Easy to operate: Conveyor systems are easy to operate and require minimal training.
Automated controls: Conveyor systems can be controlled through automated systems, reducing the need for manual intervention.
Advantages
Increased efficiency and productivity: Conveyor systems automate the movement of materials, increasing efficiency and productivity.
Reduced labor costs: Conveyor systems reduce the need for manual handling of materials, reducing labor costs.
Improved safety: Conveyor systems reduce the risk of injury by reducing the need for manual handling of materials.
Increased speed: Conveyor systems can move materials quickly and efficiently, increasing production speed.
Improved quality control: Conveyor systems ensure consistency in the movement of materials, reducing errors and improving quality control.
Reduced waste: Conveyor systems can be designed to minimize waste by ensuring materials are moved efficiently.
Scalability: Conveyor systems can be easily scaled up or down to meet changing needs and requirements.
Space-saving: Conveyor systems can be designed to fit into small spaces, maximizing floor space.
Energy-efficient: Conveyor systems can be designed to be energy-efficient, reducing energy costs.
Customization: Conveyor systems can be customized to fit specific needs and requirements.
Integration: Conveyor systems can be integrated with other equipment such as robots and sensors to create a fully automated system.
Low maintenance: Conveyor systems require minimal maintenance and can operate for long periods of time without interruption.
Cost-effective: Conveyor systems can be a cost-effective solution for material handling, reducing labor costs and increasing efficiency.
Versatility: Conveyor systems can be used to transport a wide range of products and materials.
Improved customer satisfaction: Conveyor systems can improve customer satisfaction by ensuring products are delivered quickly and efficiently.
FAQs
What is a conveyor system?
A: A conveyor system is a mechanical system used to transport products or materials from one place to another.
What industries use conveyor systems?
A: Conveyor systems are used in a wide range of industries, including food processing, automotive, pharmaceuticals, and more.
What are the advantages of using a conveyor system?
A: The advantages of using a conveyor system include increased efficiency and productivity, reduced labor costs, improved safety, increased speed, improved quality control, reduced waste, scalability, space-saving, energy-efficient, customization, integration, low maintenance, versatility, and improved customer satisfaction.
What are the different types of conveyor systems?
A: The different types of conveyor systems include belt conveyors, roller conveyors, chain conveyors, screw conveyors, pneumatic conveyors, overhead conveyors, vibrating conveyors, bucket conveyors, magnetic conveyors, and spiral conveyors.
What are the disadvantages of using a conveyor system?
A: The disadvantages of using a conveyor system include initial costs, maintenance costs, limited flexibility, limited mobility, and noise pollution.
Can conveyor systems be customized?
A: Yes, conveyor systems can be customized to fit specific needs and requirements.
How can conveyor systems be energy-efficient?
A: Conveyor systems can be designed to be energy-efficient by using efficient motors and reducing friction in the system.
What is the difference between a belt conveyor and a roller conveyor?
A: Belt conveyors use a belt to transport materials while roller conveyors use rollers to transport materials.
What is a screw conveyor?
A: A screw conveyor is a type of conveyor system that uses a helical screw to transport materials.
What is a pneumatic conveyor?
A: A pneumatic conveyor is a type of conveyor system that uses compressed air to transport materials.
What is an overhead conveyor?
A: An overhead conveyor is a type of conveyor system that uses an overhead track to transport materials.
What is a vibrating conveyor?
A: A vibrating conveyor is a type of conveyor system that uses vibrations to transport materials.
What is a magnetic conveyor?
A: A magnetic conveyor is a type of conveyor system that uses magnets to transport materials.
What is a spiral conveyor?
A: A spiral conveyor is a type of conveyor system that uses a spiral track to transport materials.
What is the maximum weight a conveyor system can handle?
A: The maximum weight a conveyor system can handle depends on the type of conveyor system and its design.
Can conveyor systems be used in hazardous environments?
A: Yes, conveyor systems can be designed to operate in hazardous environments with proper safety measures.
How are conveyor systems powered?
A: Conveyor systems can be powered by electric motors, hydraulic systems, or pneumatic systems.
What is the difference between a horizontal and a vertical conveyor?
A: A horizontal conveyor moves materials horizontally while a vertical conveyor moves materials vertically.
What is the difference between a single-chain and a double-chain conveyor?
A: A single-chain conveyor has one chain while a double-chain conveyor has two chains.
What is the difference between a flexible and a rigid conveyor?
A: A flexible conveyor can bend and curve while a rigid conveyor is fixed in a straight line.
In conclusion, conveyor systems are an essential part of material handling in various industries. They offer many advantages, including increased efficiency and productivity, reduced labor costs, improved safety, and increased speed. There are many different types of conveyor systems, each with its features and advantages. While there are some disadvantages to using conveyor systems, such as initial cost and maintenance, the benefits often outweigh the drawbacks. Overall, conveyor systems are a cost-effective solution for material handling that can improve the bottom line for businesses of all sizes.
Email: Sales@magnatechengg.com
Tel: +97143404243
Mobile: +971 55 633 8365
[…] cost: The initial cost of purchasing and installing a conveyor system can be […]
[…] that is designed to enhance the efficiency of material movement in a wide range of industries. This conveyor system features a broad body that provides ample space for conveying different sizes and shapes of […]
[…] The food industry is highly regulated to ensure that the food that reaches the consumer is safe and of good quality. As a result, food safety inspections are conducted at various stages of the food production process. One of the critical steps in the inspection process is ensuring that the food is free from contaminants, foreign objects, and other impurities. This is where the Meals Inspection Conveyor comes into play. This article will discuss the benefits and drawbacks of using this technology in the food industry. […]
[…] As businesses grow, the conveyor system can be expanded to accommodate higher volumes, offering scalability and […]
[…] handling bulk tea powder efficiently can be challenging. That’s where the specialized conveyor for bulk tea powder comes in. Its unique design ensures gentle handling, preventing damage to the […]
[…] Connectivity: The conveyor could be integrated with smart home systems, enabling users to control and monitor their omelette […]
[…] Downtime: With its robust construction and reliable components, the Modular Belt Curve Conveyor ensures minimal downtime, leading to increased […]
[…] Product Loss: Conveyors can reduce product loss during transportation, increasing profits for bottling […]